Travertine Flooring
Travertine Flooring
Restoration of Tile, Stone, Concrete, Carpet Floors for Coachella, Palm Springs, Palm Springs, Rancho Mirage, Palm Desert, Indian Wells, La Quinta, Indio and for the rest of the Coachella Valley.
TR Floors is a professional stone cleaning and restoration company that specializes in services ranging from performing routine maintenance on stone floors and granite counter tops to solving complex tile, grout and stone problems. Our Partners combined have been in the floor restoration business for over forty years and with our knowledge, we can help you to preserve and maintain your investment of lasting beauty in natural stone.
Travertine Flooring Information Overview
Travertine Flooring Information Overview
- No rust color should be in the color of the stone
- No pores should be in the filling of the stone
- No rust colors should be in the pours of the stone in the back
- The filling should be filled with cement (each tile goes through a mechanical filling process, then re-inspected and filled once again by hand)
- The cit on the sides should be perfectly perpendicularly cut and no slope is acceptable
- The thickness of the tile should be in inches
- The color variation of the lot of the tile should be as close as possible without noticing the color variation and consistency
- The tile should measure (12"-12", 16"-16", 18"-18" & 24"-24")
- The cut of the block should be cross vain cut and not straight cut
- The crates should be build from strong wood pallets and to the specifications needed for stacking and fork lift use
- The face of the tile should show from both sides of the crate
- The tiles should be packed in a special way where the face of the finished tile will be facing forklift use
- There should be Styrofoam on the bottom of crate and side of tiles for protection
Travertine is a natural stone that is common to parts of southern Europe, notably Italy, Greece, and Turkey. Formed by underground rivers, springs and other types of subterranean moisture, travertine is a smooth and porous stone characterized by it rich creamy hue. Great civilizations of the ancient world relied upon travertine as a staple building material for use in the creation of their most notable and ornate architectural accomplishments, including the famous Roman Coliseum.
This is a testament not only to the illustrious history of travertine, but also to its longevity, timelessness and durability. Today, travertine embodies a classical beauty, and remains to be a common building material in Italy. Premium travertine tile flooring is becoming more and more popular for both homes and commercial buildings for these reasons. This premium tile is a classy choice, rich in appearance and practicality. Travertine is a tasteful choice for your tile floor project.
Travertine tile flooring can add an extremely elegant touch to any space, and the premium travertine tile can be the defining touch in color and texture for many of applications.
The white stone that you see all over Rome, from the fountains to the old noble palazzos and from St. Peter's church to the Colosseum, is almost always travertine rather than marble. Although travertine looks porous, with its gaps, bubbles, grain, and inclusions, the stone actually is much less permeable than marbles, limestones, and sandstones.
It is not as strong and impermeable as granites or basalts, but it is much cheaper because it is more easily quarried and worked and much more available. It has been the structural stone of choice in Rome for 2000 years because it is stronger than marble and because one of the largest deposits of good travertine in the world is just twenty miles down the road at the base of the Tiburtine mountains.
Travertine is a product of the earth's water and carbon cycles. As carbon dioxide-rich rainwater percolates through soil and stone, it slowly dissolves tremendous quantities of limestone along underground fissures. This water, now saturated with dissolved limestone, reemerges at the surface at warm or hot springs and releases carbon dioxide gas into the atmosphere -- much like carbonated mineral water.
Once the carbon dioxide is released, the limestone can no longer remain in solution.
It re-crystallizes, typically as the water cascades over organic films made of bacteria, algae, and mosses. A dense, banded carbonate stone is built up over time as new material covers older layers. This process has continued at the Bagni di Tivoli springs for at least 80,000 years. (This is the same process that builds up the terraces around the springs at Yellowstone National Park in the United States. The "yellow stone" there is fresh sulfurous travertine of almost the exact same chemical composition as Bagni di Tivoli stone.)
Calcite and gypsum, the minerals that make up about 99 percent of travertine stone, are colorless. The beautiful honey color of Tivoli travertine is from the other 1 percent of the stone: traces of yellow sulfur, brown iron compounds, and organic pigments. The intricate "Swiss cheese" texture of travertine is partly the result of gas bubbles, which are often trapped between layers of stone, creating spherical voids.
Minerals crystallizing on the ever-present bacteria in travertine deposits -- like granular snow blanketing a miniature landscape -- preserve organic growth forms, called "shrubs," and produce much of the rugged relief evident if the stone is split for use along its "grain". In some cases, travertine layers are similar to tree rings, with lighter and darker laminations representing seasons of growth.
Travertine is found in greatest abundance where hot and cold springs have been active for tens of thousands of years. The most famous travertine location, is Bagni di Tivoli, 20 kilometers east of Rome, where travertine deposits over 90 meters thick have been quarried for over two thousand years. The name of the stone is, in fact, derived from the ancient Roman name of Tivoli, which was Tibur. "Tibur stone" in Latin was "lapis Tiburtinus", which with only a little corruption became "Travertine".
Because travertine is plentiful, weighs less than marble or granite, and is relatively easy to quarry, it was the stone most commonly used by the ancient Romans. Famous structures constructed with Tivoli travertine include the Colosseum, the Trevi Fountain, the façade and colonnade of Saint Peter's Basilica, and many Roman aqueducts. In the last century, Lincoln Center in New York and the ABC Entertainment Center in Los Angeles were faced with travertine from the same Tivoli quarries.
Travertine is split with the grain of the stone, making visible many more fossils than are seen in the more common banded travertine, which is cross-sectioned and polished. At least two species of fossilized leaves are fairly common in stone from Bagni di Tivoli -- evidence of a lakeside environment at the time of the stone's formation. Fossilized animal material is less common, but an occasional feather or bone is discovered. The rapid deposition of the travertine layers acts as a natural preservative for these traces of prehistoric life.
In order to remove the travertine from the vertical quarry face, workers drill holes into the stone, outlining a block 6 meters high, 12 meters wide, and 2 meters deep. A diamond-studded cable is then threaded through the holes, lubricated with water to prevent heat buildup, and pulled against the stone with a set of pulleys. A large cut may take a day and a half, but eventually diamond wins out over the softer travertine.
When the cuts are completed, the slab is pushed away from the quarry wall and falls onto mounds of earth, which help cushion the fall. The slab is then broken up into more manageable cubes, which are taken to factories for honing and cutting or splitting. An automated guillotine has been invented to split the stone along its natural bedding plane, or diamond saws can be used to cut standard or specially ordered cross-cut stones and slabs.
Travertine floor surfaces are anticipated to last at least 50 years before replacement or refinishing is needed in high-traffic areas. High-quality travertine is very durable, since it is formed at the earth's surface in relative equilibrium with the environment. Most other building stones are formed under different conditions, deep underground and may be less stable in surface temperature and pressure conditions.
In modern installations, travertine blocks may be treated with silicon-based water repellents that are expected to ease cleaning. Paving stone and lower parts of walls in public areas may also be treated with oil and paint resistant coatings to reduce the effects of soiling and graffiti. It's important, however, not to completely seal surfaces since that could cause moisture to accumulate inside the stone or to migrate to inner walls where it could damage plaster or stucco surfaces or frescoes. Man-made travertine can also be acquired.
Recent Restoration of Travertine
Recent Restoration of Travertine
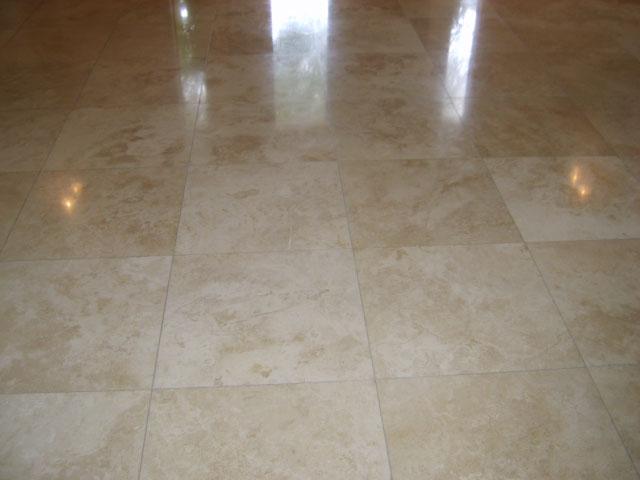
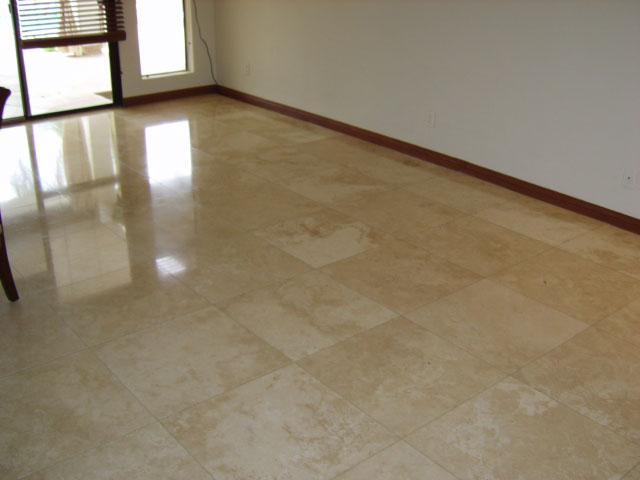
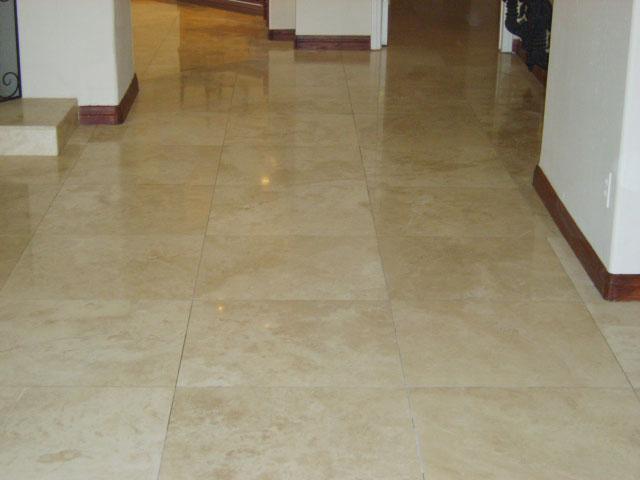
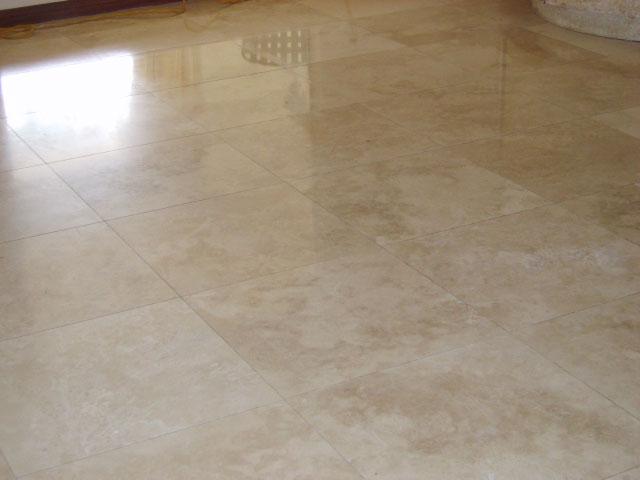
To clean the floor, the floor is first washed with a floor machine with special pads. After the washing procedure, and after the floor is totally dry, a polishing procedure, if required, will be completed.
After the floor is totally dry, a sealing procedure will be completed. Foot traffic will be allowed after 6 hours
To Restore Floor from Scratches
To Restore Floor from Scratches
For Example; Scratches are Deep on Surface. (High Traffic Area)
Recommendation; Hone & Polish
Overview:
Hone: Scratch removing by wet grinding with diamond pads. (A satin finish with little or no gloss). Must be further processed Totally shine.
General Direction for Grinding Instructions (always use a professional)
To achieve a good result in grinding and polishing marble, Terrazzo, Limestone, Travertine etc.
A 15" to 20" floor machine should be used.
The grinding should begin near the walls, proceeding then gradually towards the center.
The machine must work Parallel to the wall. This way the borders can be level much easily, and the machine can absorb the shocks caused by the roughness of the floor without knocking against the wall.
It is very important that the borders near the wall be leveled carefully, to prevent damaging of finer grits against a lippage in the floor, and to avoid the long and never-quite-perfect work of smoothing them by a hand grinder.
It is very important to choose the right diamond, bond and shape to match the requirements of the work to be done.
The machine must never stand stationary in one spot when the motor is running. Use a medium swinging motion.
Do not grind stone without water (dry). you can burn the stone (If this happens the damage is non - reversible).
Always be sure to apply water before starting the machine. Do not use to much water. In tests for the optimal amount of water verses time, It has been determined that it is better to pour small amount of water on the low grits, and increase the water supply when using higher grits.
When getting to low point (dips) in the floor, it is important to grind with a round movement to level a bigger portion of the floor to hide the wave. The waves will be more noticeable after polish.
When grinding a high lippage floor it is better to grind from the high point towards the low point to protect your diamond and to protect the high cornerstone (from chipping or collapsing).
Grinding: 30 to 50 grit *(120 Grit)
- Cut (Lippage) to level the surface.
- Lippage removal diamond.
- Resin bond diamond.
- Metal bond diamond.
- Classic Carbide stones.
- Install the first cutting tools 1/2" from the edge (inside).
- (Cutting tools or lippage removal should be tapered at the edge.)
- Use 120 grit cutting tools for very delicate or vain Materials.
- When cutting a high lippage, work from the high level to the low (to protect your cutting tools).
- Work the machine all the way to the walls.
- Water: start the cutting with a very wet past like.
- Erase the cutting scratches.
- Resin bond diamond.
- Metal bond diamond.
- Classic Carbide stones.
- This time we will put the diamond only 1/4" from the edge, to make shore we remove all the cutting scratches.
- P.S. It is very important to rinse the surface between every grit, to remove all the last grit remains.
- Water: every higher grit add more water.
Polish: 400 to 600-800 grit.
- Depending on the materials finish with low (600) grit on hard & high (800) grit on soft.
- Resin bond diamond
- Classic carbide stones.
- This time we put the diamond all the way to the edge, to erase all remain honing scratches.